Metsä: Fossil free steam production for tissue production
Since September this year Metsä Tissue Kreuzau mill is replacing the use of fossil-based lignite by wood pellets. So far, the papermaking process requires an annual emission of 90tk CO₂. By implementing wood pellets instead of lignite, fossil-based CO₂ emissions are reduced by 60 kt per year means Metsä Tissue’s Kreuzau mill compares favourably with the EU Emissions Trading Scheme (ETS): the emission level at Metsä Tissues Kreuzau mill is 200 kg CO₂/tn compared to the benchmark of 340 kg CO₂/tn. With this step Metsä is further executing the transition to a fossil-free production by 2030 as well as delivering world-class environmental performance. This transition has been initiated by a simple idea to change fuels, but keeping the existing technical infrastructure. Since beginning of 2022 the shift to wood pellets has been tested, necessary adaptions were made and now the shift has been finalized.
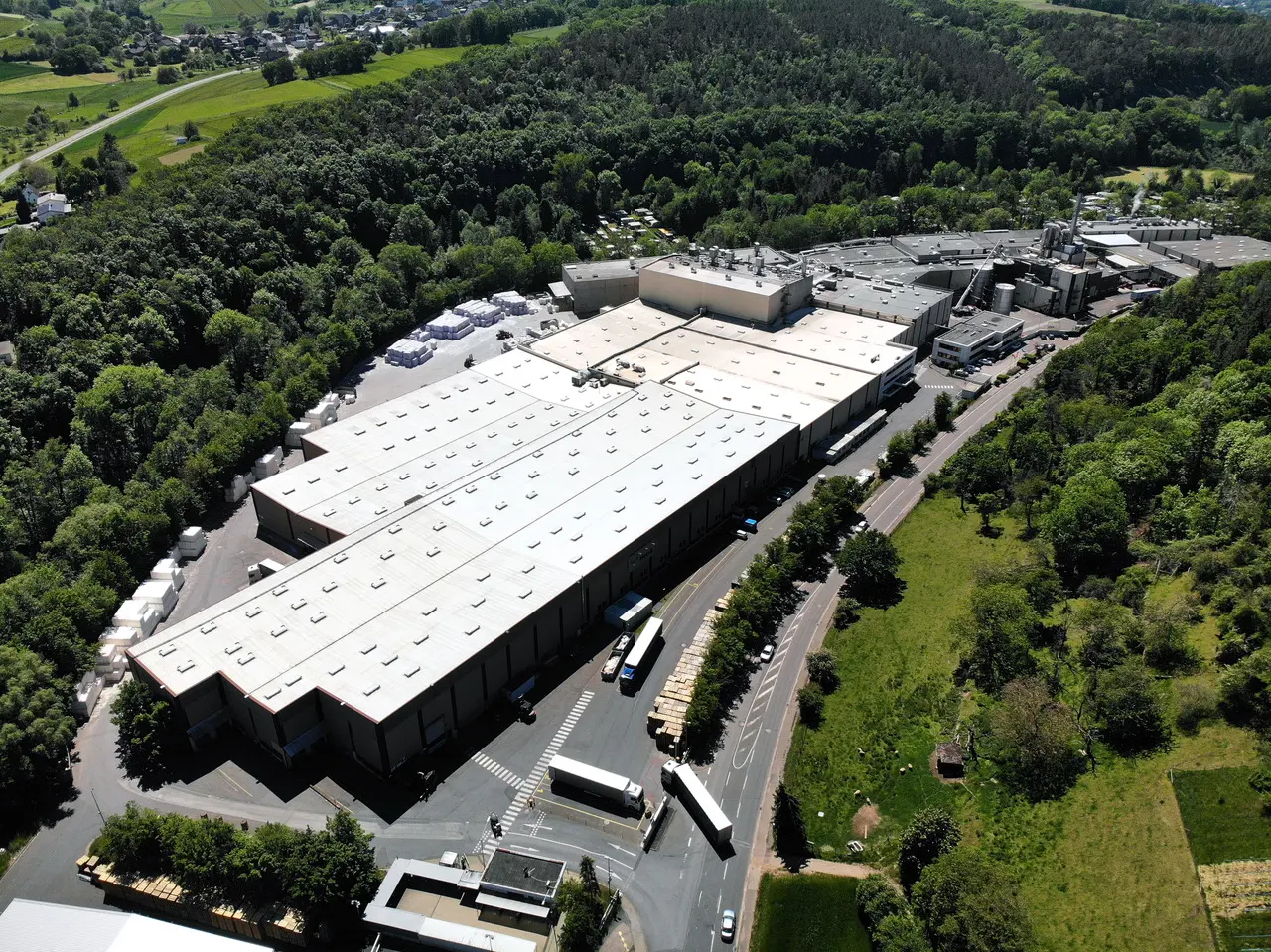
Goals
As part of Metsä Tissues strategic goals the company strives to have fully fossil free production by 2030. The wood pellets replace now the use of fossil-based lignite/charcoal, supporting Metsä Group's and Metsä Tissue's sustainability goals as well as the German government's phase-out of coal-fired power generation. Although this fuel shift applies to Metsä Tissue’s Kreuzau mill, we will continue to develop towards a sustainable future technology in all Metsä Tissue mills.
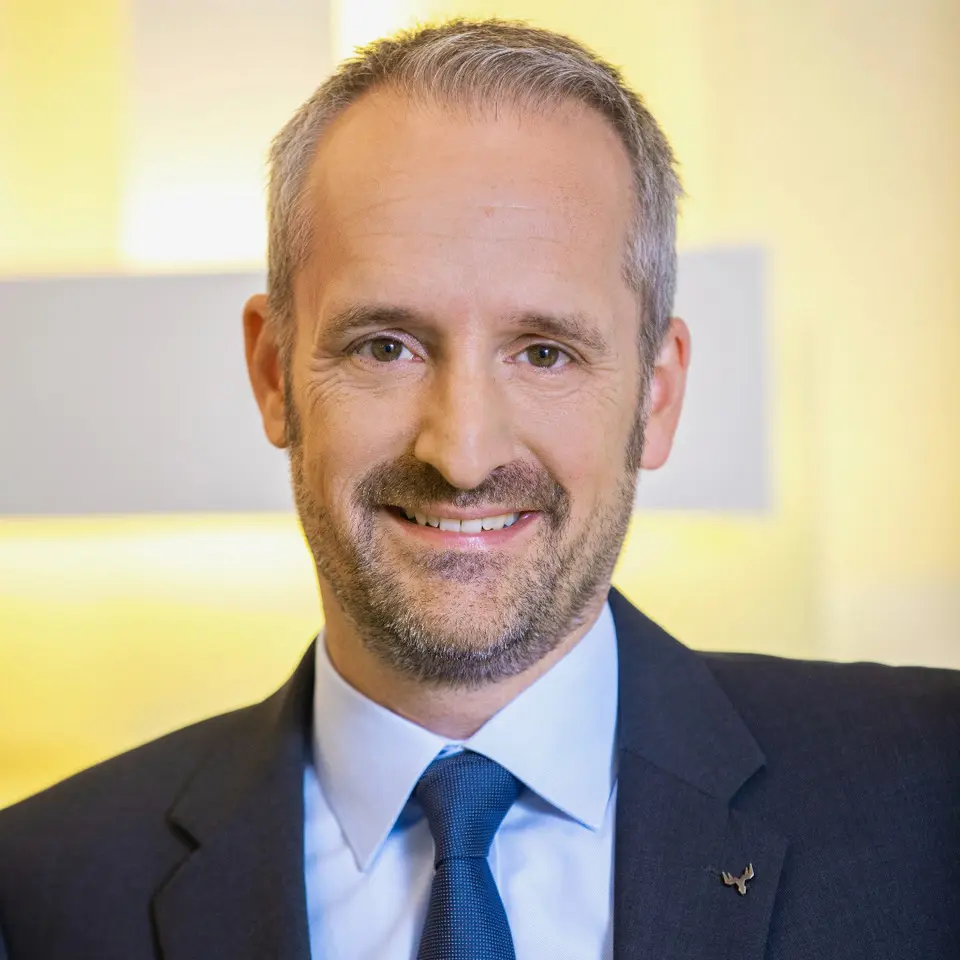
“Metsä Tissue as part of Metsä Group, is investing to reduce CO₂ emissions and to achieve our 2030 goal of completely fossil-free mills. At the same time it requires the right framework conditions e.g. industrial bridge electricity prices to be able to remain competitive.”
• Fossil-based CO₂ emissions are reduced by 60 kt per year, which equals 2/3 of annual CO₂ emission level at Kreuzau mill.
• Kreuzau mill compares favorably with the EU Emissions Trading Scheme (ETS): The emission level is significantly below benchmark: 200 kg CO₂/tn compared to the benchmark of 340 kg CO₂/tn
• By using existing technologies in combination with adapting efforts, the positive savings effect could be proven over a test phase starting at the beginning of 2022.
MORE LIGHTHOUSES
.jpg)
WEPA produces hygiene paper from the sustainable fibre innovation of recycled carton
After years of research and development, we have succeeded in preparing recycled carton in such a way that we can use it as raw material for our hygiene paper production.
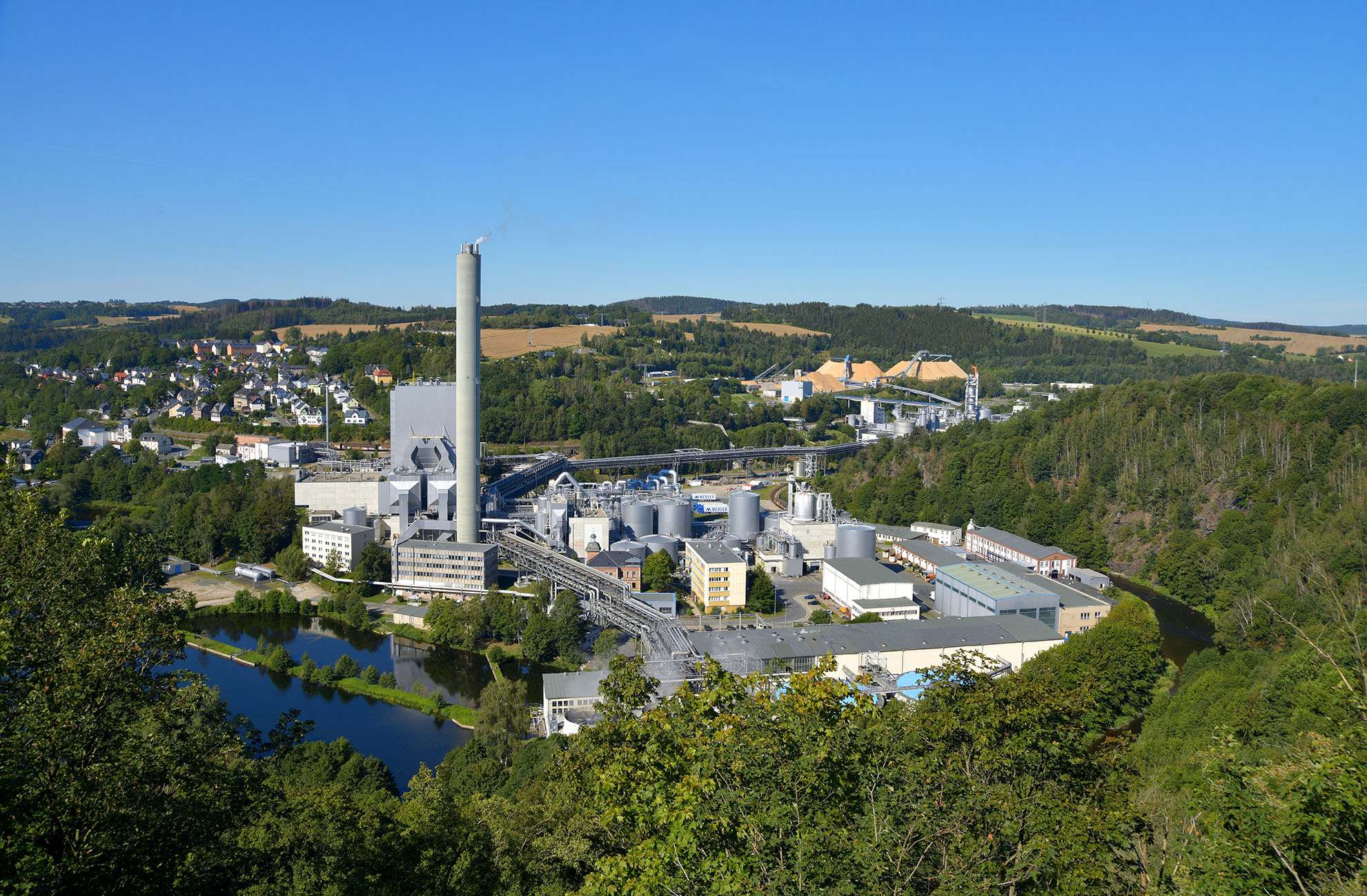
Mercer Rosenthal GmbH Adds Stripper to Evaporation Plant to Optimise Resource Use
A stripper has been added to the existing evaporation plant in order to separate the usable material of the B-condensate from the liquid.
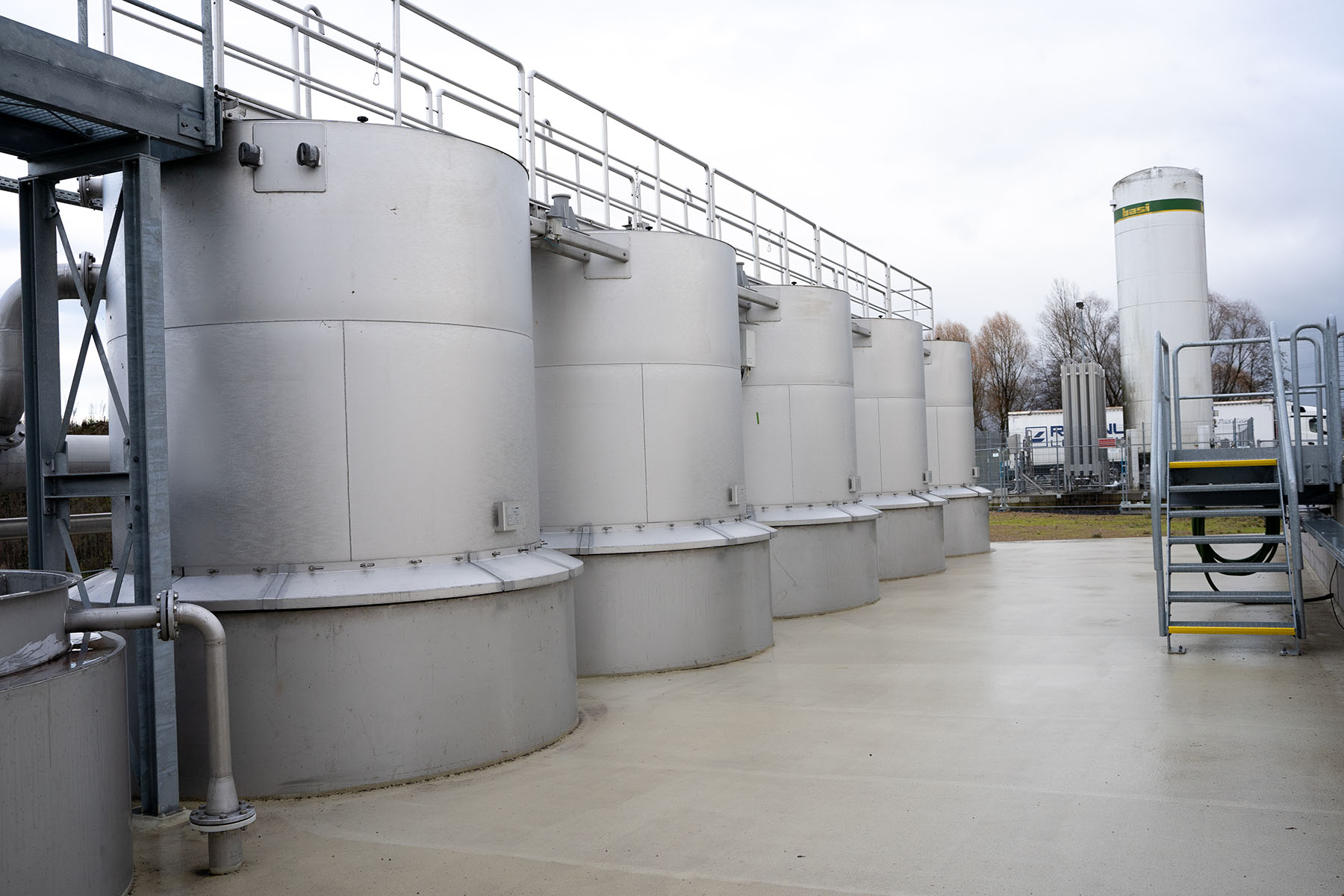
Expansion of the Wastewater Treatment Plant at Koehler Paper's Kehl Site
In early 2024, after 1.5 years of construction work, the Koehler Paper site finalised the expansion of its wastewater treatment plant. This expansion had been initiated because of the construction and activation of Production Line 8 in 2019, and the attendant increase in wastewater volume.
Enhancing Efficiency: SAPPI Alfeld GmbH Upgrades Wastewater Treatment with Advanced Flotation Cells
As a direct discharger into the Leine, SAPPI Alfeld GmbH has for decades internally run a complete water treatment with a three-lane biological stage.
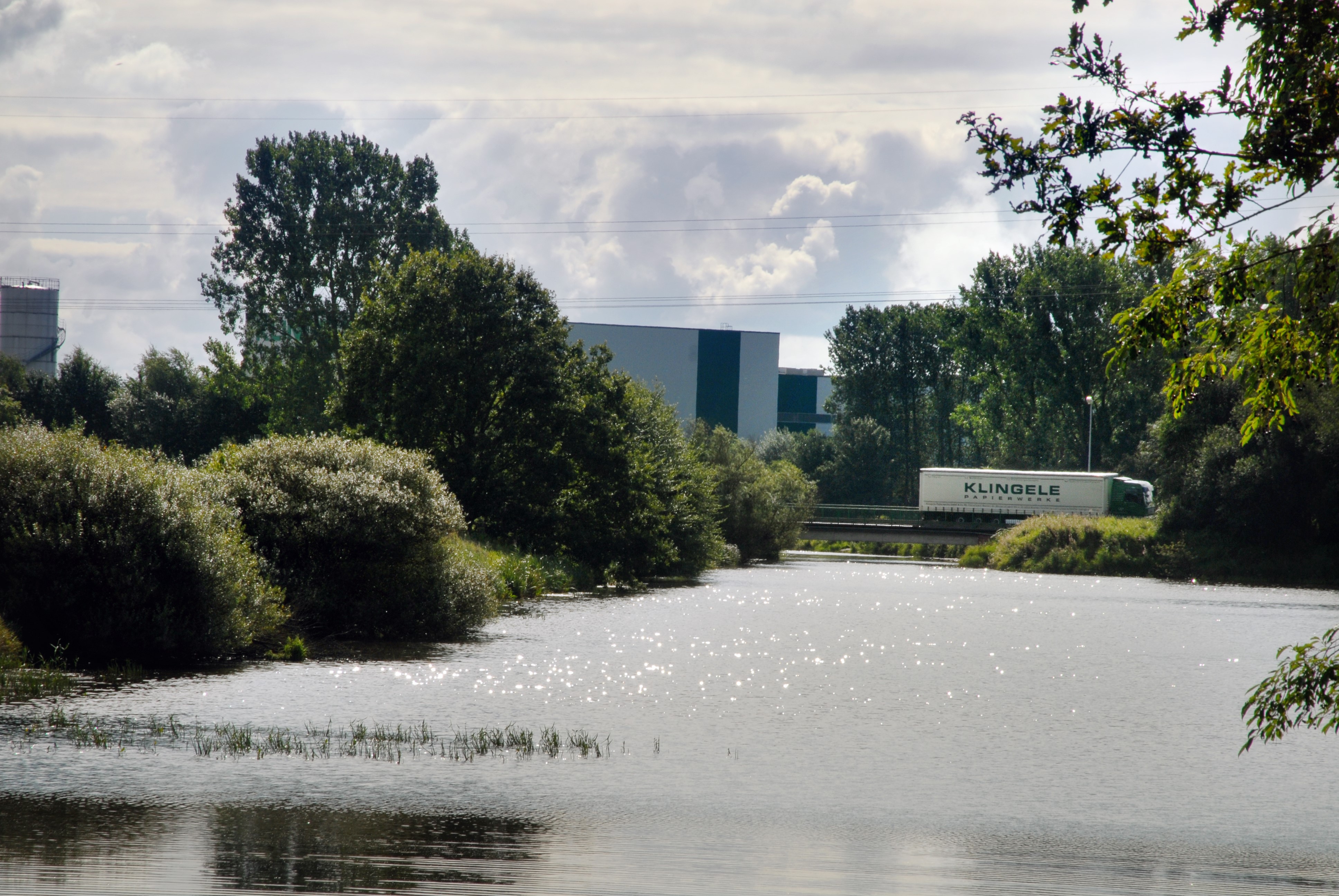
Smart Water Management: Sielacht Rheiderland Implements Real-Time Data-Driven Volume Control System
The water volume management concept for Sielacht Rheiderland involves both data collection as well as the creation of a management concept for the waters of the Siel.
Felix Schoeller: Installing a Disc Filter at PM4 in Weißenborn to Drive Sustainability Goals
Installing a disc filter at the PM4 in Weißenborn. Integrating the disc filter with the sieve water system as well as the technological plant control.
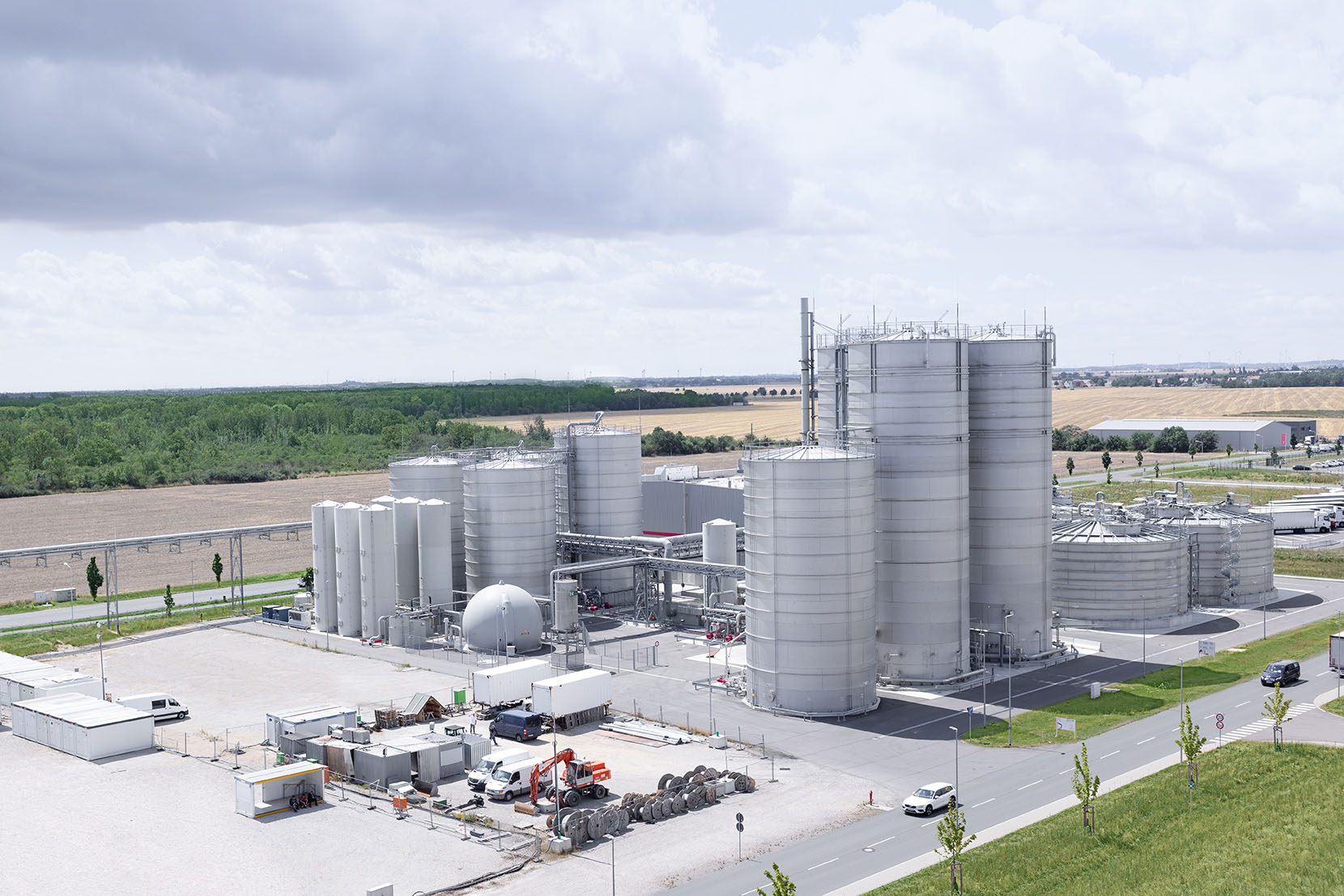
Progressive Water Recycling Treatment at Progroup: 80% Reduction of Freshwater Use in Paper Production
In August 2020, Progroup put the high-tech paper factory PM3 in Sandersdorf-Brehna into operation. It ranks among the most modern and productive factories of its kind worldwide, with an annual production capacity of 750,000 tonnes of corrugated base paper.
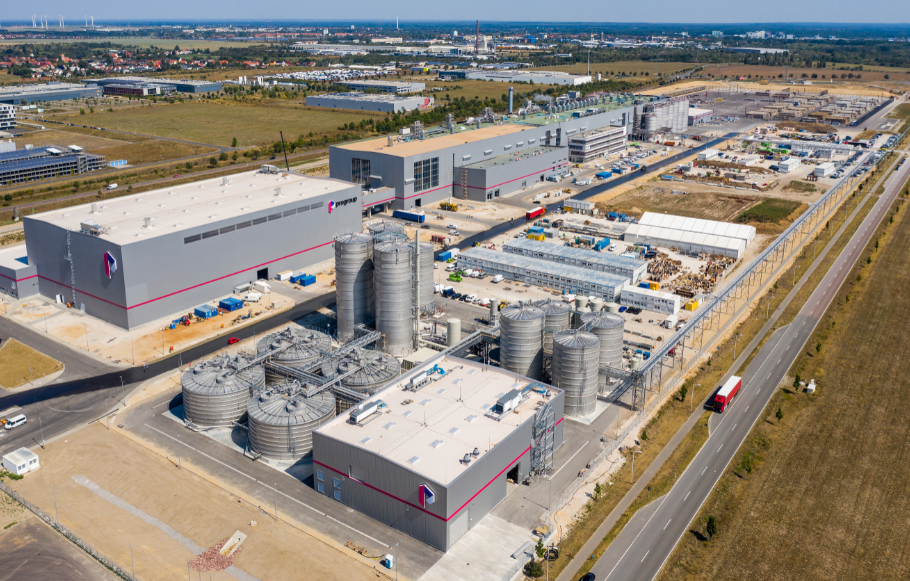
Resource-efficient circular economy in practice: PROGROUP upgrades its manufacturing facilities to zero-waste status
In August 2020, Progroup opened the high-tech PM3 paper mill in Sandersdorf-Brehna near Leipzig. It is one of the most modern and efficient in the world.
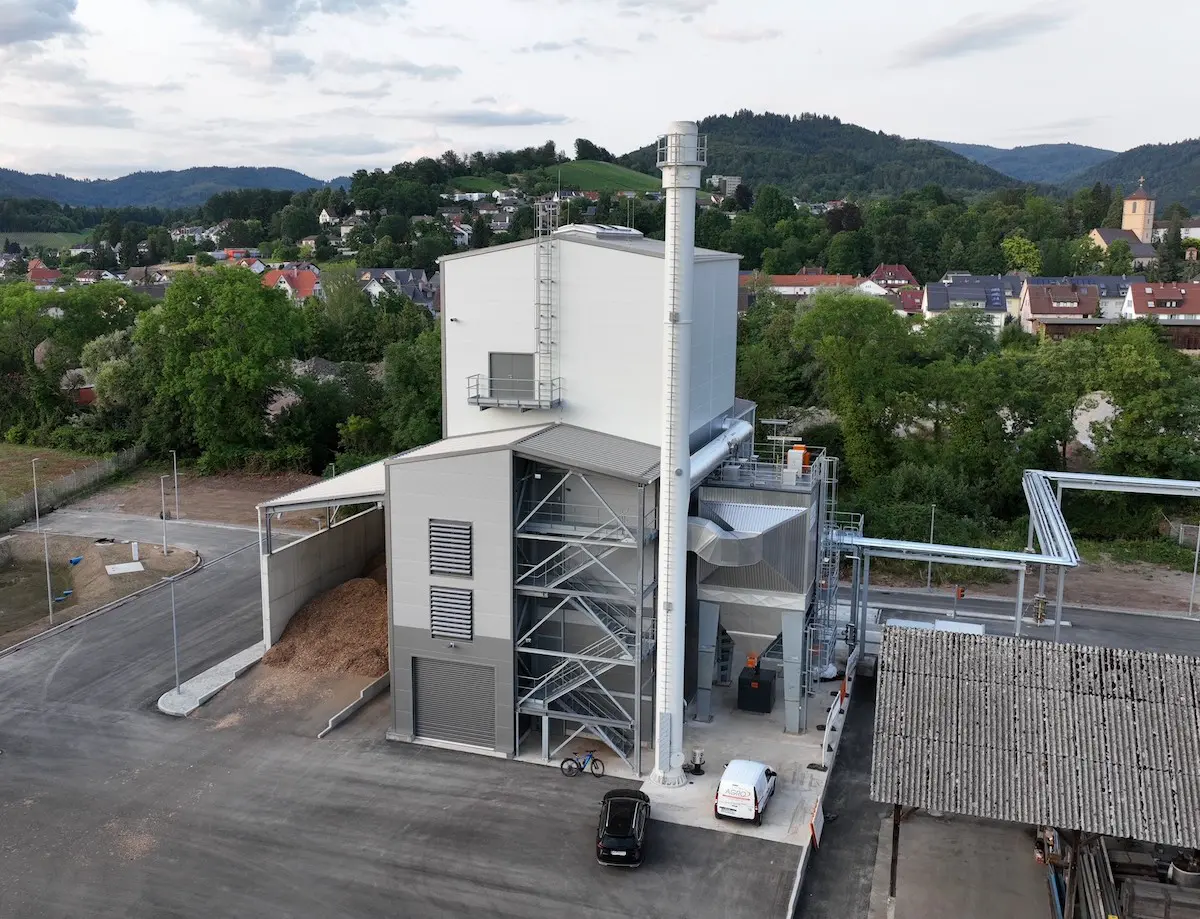
Biomass replaces lignite dust at Köhlerpappen GmbH in Gengenbach
In 2020, the German government decided to impose a CO₂ levy on all fossil fuels, with effect from 2021. For Köhlerpappen GmbH, Gengenbach, this means that significant additional costs will be incurred from 2023 onwards.
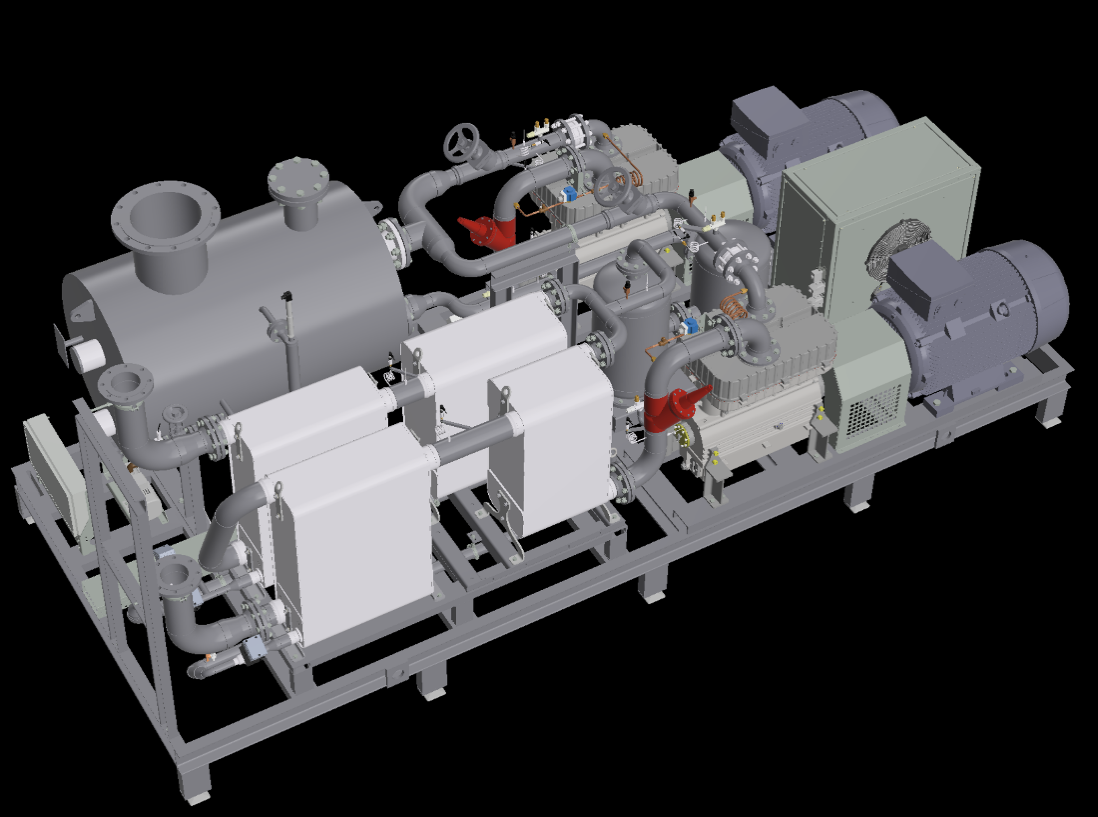
Push2Heat: Felix Schoeller installs the Group’s first high-temperature heat pump at its Weissenborn plant
In the framework of the EU-funded Push2Heat project, four demonstration plants are being planned in Europe in a collaboration of international partners and research institutes.
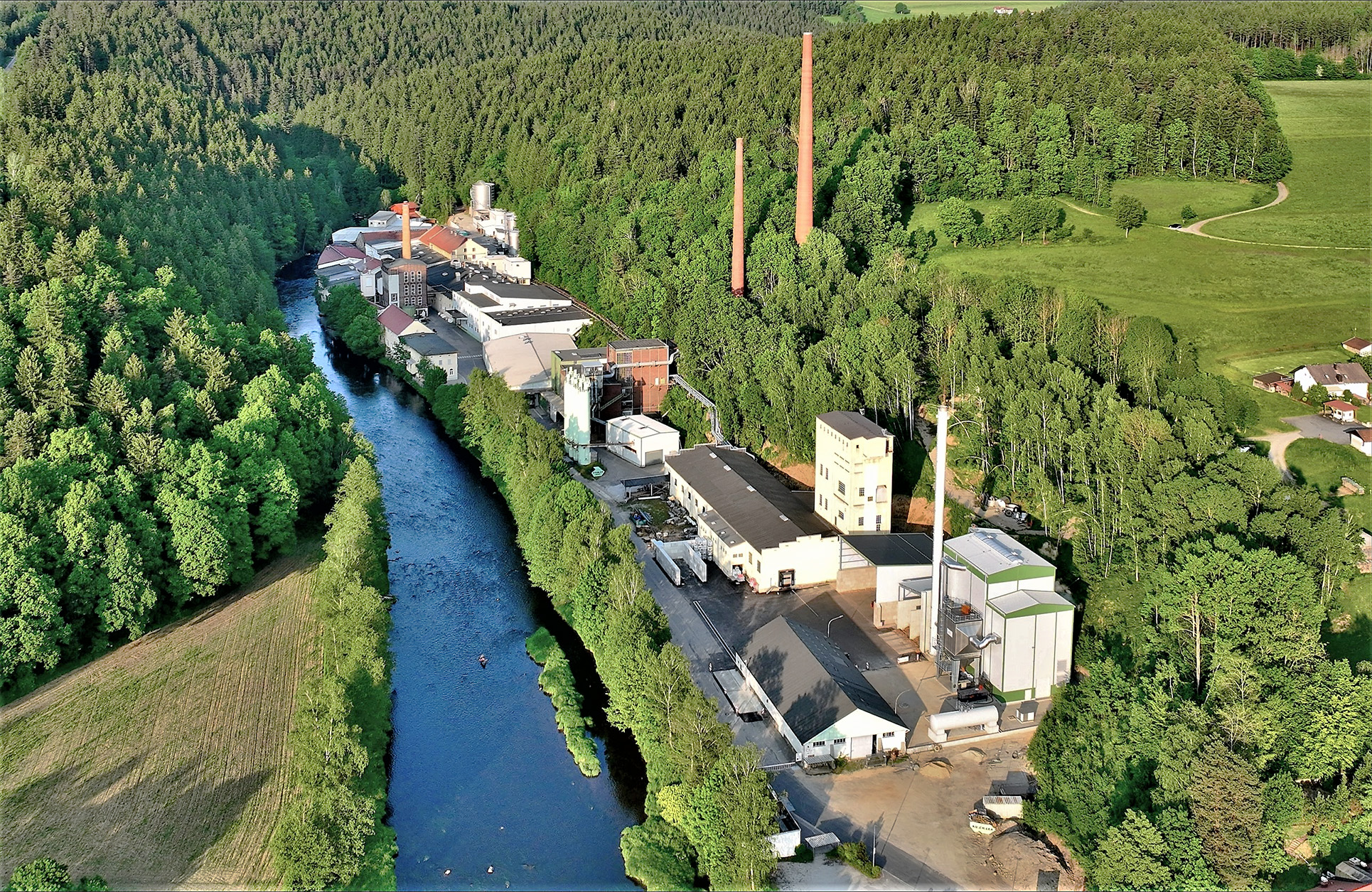
Pfleiderer switches fuel for steam generation from pulverised lignite to biomass
The aim of the project is to build a modern biomass power plant to supply the entire heat requirements of the Pfleiderer Spezialpapiere paper mill while reducing the previous CO₂ emissions by approximately 27,000 tonnes per year.
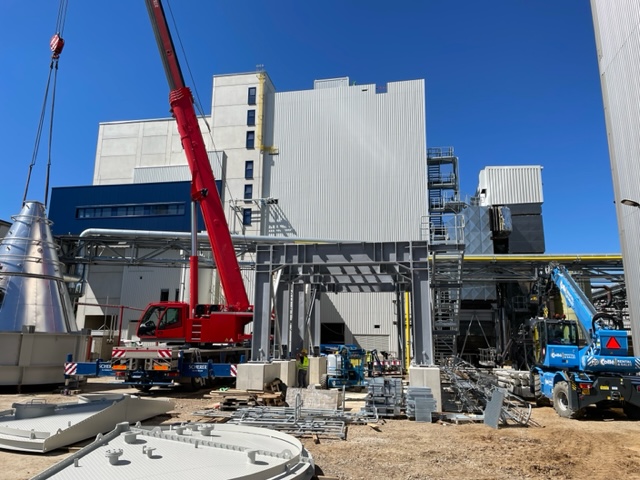
Ultra-efficient CHP plant together with recycling of residual materials delivers sustainable heat supply at SCHOELLERSHAMMER
The Energy Supply 2024 project was launched to transform and secure a sustainable energy supply.
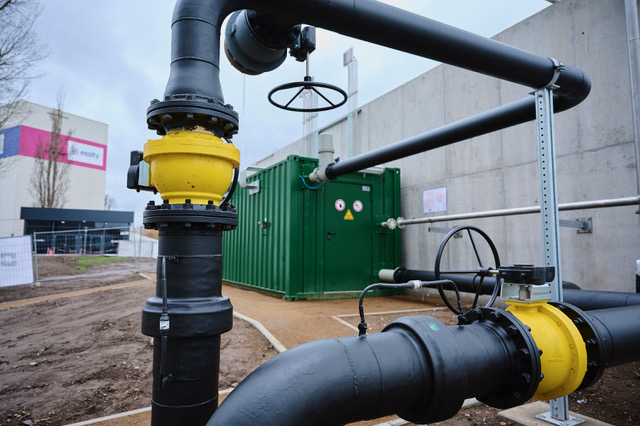
CO₂-free production of hygiene papers at Essity
At its mill in Mainz-Kostheim, leading hygiene and healthcare multinational Essity has become the first company to succeed in the CO₂-free production of paper. This has been made possible by reducing energy consumption, powering the paper machine with electricity from renewable sources and using green hydrogen.
.webp)
PALM power plant innovation programme: On the way to CO₂-neutral paper production
At its three sites in Germany, PALM operates gas-fired power plants according to the CHP (combined heat and power) principle.

UPM electrifies heat supply, supports expansion of renewables and boosts system stability
UPM is investing in e-boilers (electrically powered steam generators) at four of its current six sites in Germany. When renewable electricity is available in sufficient quantities, these can take over steam generation for paper production at competitive prices, thereby economising on natural gas.
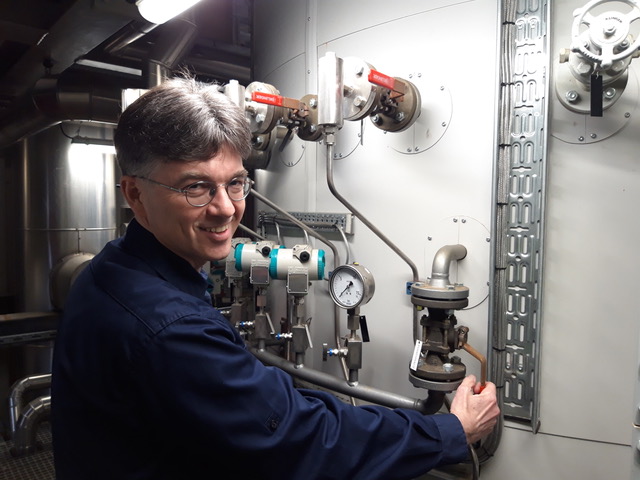
Varel trials climate protection module: Wind power generates steam for paper machines
Clean wind power is an important building block in working towards climate neutrality – but what if there is too much power in the grid?